Electric Vehicle Industries
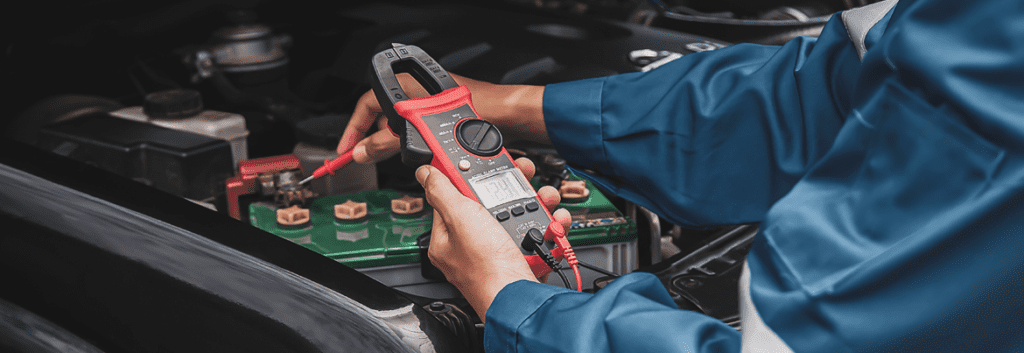
Case studies
1. BMS – Battery Management System
Monitoring Parameters:
- Voltage
- Temperature
- Current
- Calculation of Charge/Discharge Limits
- State Monitoring: SOC, SOH, and SOF( state of charge, state of health and state of function)
Communication Protocols: Integrating multiple communication protocols poses compatibility and reliability challenges, crucial for seamless data transfer and effective BMS operation.
Control Mechanisms: Implementing effective protection mechanisms and advanced control strategies is critical for battery safety and operational efficiency.
Solution: By deploying high-precision sensors and advanced hardware integration real-time acquisition is achieved.
Using the NI( National Instruments ) and other standard or customized hardware, LabVIEW, Veristand, Teststand, and other integration platforms the system is developed to have accurate data interpretation
Matlab / Simulink models can be integrated on NI RT platform to get precise data for next-level analysis.
With integrated CAN, and CAN FD protocols for comprehensive data exchange, the system ensures data integrity and security. As a control mechanism by implementing robust protection circuits, active cell balancing techniques, and adaptive control algorithms efficient energy management is achieved
Conclusion: The comprehensive integration of sophisticated monitoring, precise calculations and robust control mechanisms in the Battery Management System (BMS) for electric vehicles is essential. This holistic approach ensures enhanced safety, efficiency, and reliability.
2. Battery Pack Tester
The Battery Pack Tester utilizes advanced technology from National Instruments and other hardware components to provide comprehensive monitoring and testing solutions for battery systems. Designed for various industries, our Battery Pack test system ensures the safety, reliability and efficiency of battery operations. It uses CAN communication which speeds up the testing time.
Tests conducted:
- Monitor Cell and Battery Pack Voltage – Measure voltage levels across individual battery cells to ensure uniformity and detect abnormalities. Measure voltage of battery pack.
- Monitor Cell Temperature – Track temperature variations within the battery system to prevent overheating and optimize performance
- OCV Test
- Insulation Resistance test
- Fault Diagnosis: Identify and diagnose potential faults or malfunctions in the battery system for timely maintenance and repair

3. Solenoid Test system
Application Summary :-
Solenoid under test will be mounted on Mechanical assembly Provisions will be made in panel, to connect solenoid with test instruments during testing automatically. Provisions will be made to conduct following tests : 1. Diameter Test, 2. Resistance test, 3. HV test , 4. PE conductor Test, 5. Capacity test Test instruments will be interfaced with PC over RS 232 communication port. Digital Field-inputs and outputs will be connected to PLC , which will be interfaced to PC via MODBUS Ethernet.
Key Points :-
1. System is used to measure data in real time
2. An insulation resistance (IR) test measures the total resistance between any two points separated by electrical insulation. The test, therefore, determines how effective the dielectric (insulation) is in resisting the flow of electrical current.
3. Application software will be developed using NI LabVIEW development environment.
Benefits Achieved :-
1. Reduced Data Loss
2. Achieved Desired Cycle time
3. Flickering issue solved
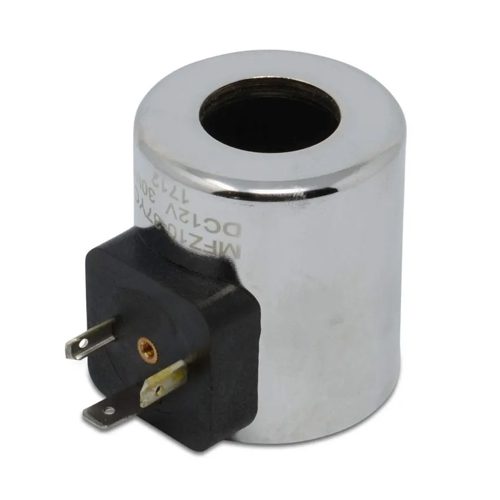
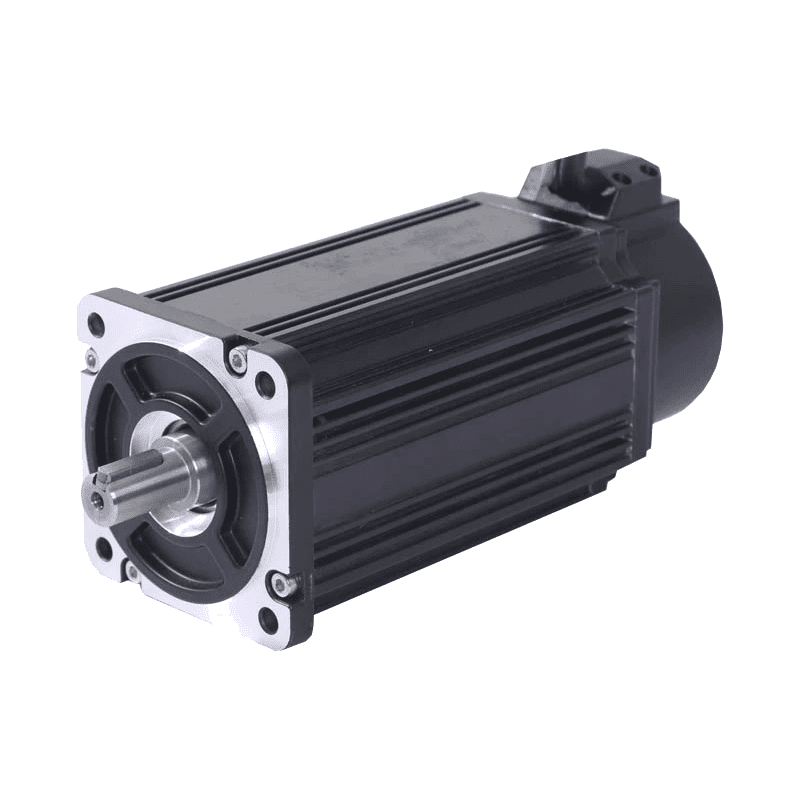
4. Endurance Test – BLDC Motors
Application Summary :-
1. Monitors and tests Multiple Units simultaneously
2. Capturs total 60 channels if all 12 devices under test are connected
Key Points :-
1. Parameters like Voltage, Current, Power, Short Circuit current, Over Load/No Load voltages, Winding losses can be tested on same test bench.
2. 11 energy meters and 12 RPM meters will communicate with the LabVIEW based customized software.
3. High speed RPM & Frequncy measurement carried out.
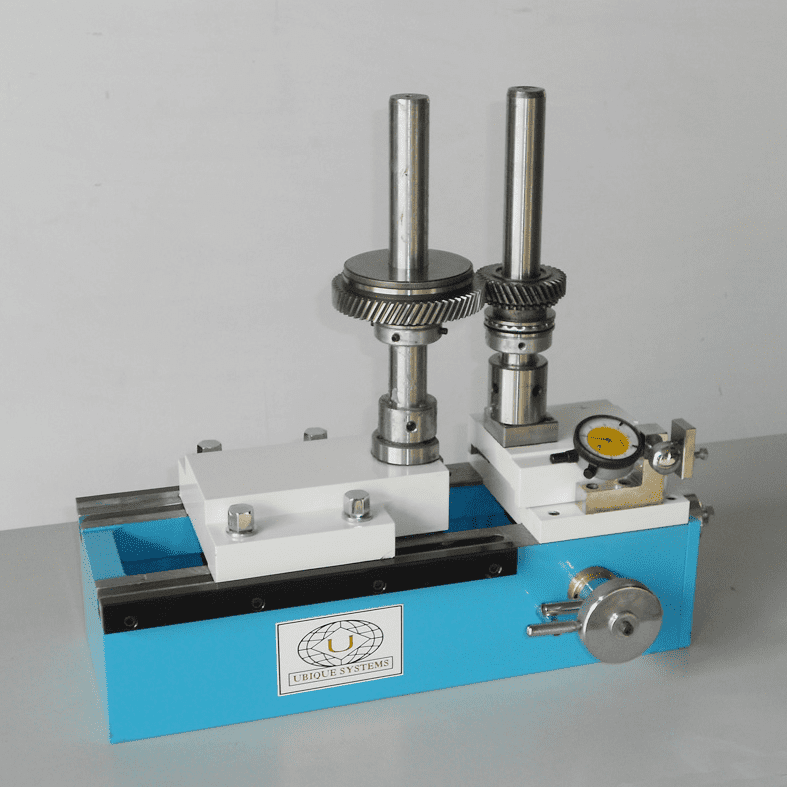
5. Gear Rolling Tester
related solutions

ATE
EOL
DAQ
LV
Panel Engineering
IIOT
ATE

ATE
Automated Test Equipment (ATE) is a machine designed for performing tests on multiple devices known as devices under test (DUT). An ATE utilizes control systems and automated information technology for performing tests that quantify and calculate a DUT in a timely manner. ATE testing is usually used in Automotive tests, wireless communication and radar as well as electronic component manufacturing. TMCS specialises in integration of offering complete system and sub-systems.
EOL

EOL (End of Line)
End-of-line Tester (EOL) systems can measure and check the functionality of automotive electronic control units, mechanical parts and related systems. Key factors considered are high test quantity, test completion and low system with upgrade costs.
DAQ

DAQ (Data Acquisition System)
National Instruments (NI DAQ) hardware based systems can be used to monitor and record various parameters during vehicle testing, such as engine performance, emissions, temperature, pressure, and vibration. DAQ systems can monitor and record data during these tests, such as load, stress, strain, and temperature measurements, to assess the durability and reliability of the components.
LV

LV (LabVIEW Development Services)
National Instruments is a technology pioneer and market leader in virtual instrumentation, a game-changing concept that has transformed the way engineers and scientists in industry, government, and academia approach measurement and automation.
Panel Engineering

Panel Engineering
Our panel range is available with different specifications in order to meet diverse requirements of the industry like Electrical Panel, control panel, power panel. Panels are designed for convenient layout and reliable wired interconnections between internal and external components.
IIOT
